Dredging Makes Sense
Billions of cubic yards of material are removed from sites around the globe annually in an effort to keep the big ships and their cargo moving. Thus, maintenance of navigation channels helps the world economy by promoting efficient trade. Our forefathers recognized this and passed the General Survey Act of 1824, which established the U.S. Army Corps of Engineers’ role as the Federal water resource agency with the primary mission for constructing and maintaining a safe, reliable, and economically efficient navigation system.
Channels are kept deep and wide enough through dredging for safe movement of ships from deep ocean waters to the more than 200 deep-water harbors where imports are unloaded and exports loaded. Dredging, performed primarily by the Corps of Engineers at navigation channels and by Port Authorities at harbors, takes place in five major areas, and the materials removed differ in consistency and placement options (numbers correspond to sample map at right):
-
Main approaches (approach channel in ocean); dredged material is composed primarily of sand.
-
Bar channels (sandbars at inlets); dredged material is composed primarily of coarse-grained sand.
-
Entrance channels (to harbors); dredged material is composed primarily of sand to fine-grained silt and clay.
-
Berthing areas (harbors/ports); dredged material is composed primarily of silt and some sand.
-
Inland waterways (intracoastal waterways and river channels); dredged material is composed primarily of silt and sand.
Dredge Types
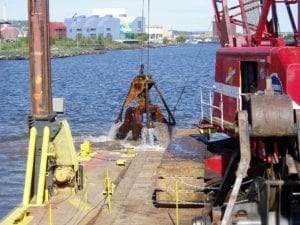
A dredge is a machine that scoops or suctions sediment from the bottom of waterways or is used to mine materials underwater. People have been dredging channels in one way or another since primitive people began to irrigate crops. Until the early 1900s, dredges were crude and barely effective in keeping channels and harbors clean. Keeping the dredge in position in the channel, knowing how deep a channel was being dug, and even making accurate surveys of the completed channel, were a mixture of art and science. Experienced dredge captains and hydrographic surveyors (surveyors of the underwater topography) were able to produce remarkably good results, given the difficulty of their job.
While the onboard instrumentation of modern dredges is computer-assisted, the basic excavation methods of dredges have remained the same since the late 1800s. The three main types of dredges are mechanical dredges, hydraulic dredges, and airlift dredges.
A hydraulic dredge works by sucking a mixture of dredged material and water from the channel bottom. The amount of water sucked up with the material is controlled to make the best mixture. Too little water and the dredge will bog down; too much and the dredge won’t be efficient in its work. There are two main types of hydraulic dredges – hopper dredges and cutter suction dredges.
A hopper dredge is well-suited for dredging materials ranging from soft mud and silt to dense sands and clay. It can maintain operations in relatively rough seas and because of its mobility be used in high-traffic areas. It is often used at ocean entrance channels and is very productive in deep water and wide open spaces. A hopper dredge is nimble and can transit quickly to dredged material placement sites under its own power without the need for tug assist or towing.
A cutter suction dredge (CSD) sucks dredged material through the intake pipe at one end and then pushes it out the discharge pipeline directly into the placement site. Since a CSD pumps directly to the placement site, it operates continuously and can be very cost-efficient. Most CSDs have a cutterhead on the suction end. A cutterhead is a mechanical device that has rotating blades or teeth to break up or loosen the bottom material so that it can be sucked through the dredge. Some cutterheads are rugged enough to break up rock for removal. A CSD is mounted (fastened) to a barge, not usually self-powered, towed to the dredging site, and then secured in place by special anchor piling, called spuds (see sidebar).
A CSD is able to work in a range of water depths and has the ability to dig its own flotation if the existing ground is very shallow or above water. It’s very efficient in areas with thick shoals, where the cutterhead is buried in the bottom. Water pumped with the dredged material is generally contained in the placement site until the solids settle out. Once settled, the water is generally returned to the waterway.
A CSD comprises the cutterhead, the spuds, the pipeline and the pontoons to float the pipeline. The connection of the spuds and cutterhead to the waterway floor, along with the floating pipeline, may sometimes limit a CSD’s ability to maneuver during inclement weather conditions.
CSD operators can adjust their approach to projects depending on the season by using anchors to help “walk” the vessel forward and efficiently utilize the floating pipeline.
A mechanical dredge removes material by scooping it from the sea floor and placing it into a barge or an approved placement area. Dipper, backhoe and clamshell dredges are types of dredges that are suitably named in accordance with their scooping buckets.
Mechanical dredges are rugged and can work in tightly confined areas. They are mounted on a large barge, towed to the dredging site, and secured in place by anchors or anchor pilings (otherwise known as spuds). Mechanical dredges are often used in harbors, near docks and piers, and in relatively protected channels. Usually two or more disposal barges, called scows, are used in conjunction with a mechanical dredge. The operation generally consists of a series of barges. While one barge is filled with material, another barge transits to the placement site and then returns to repeat the cycle, allowing for near continuous and uninterrupted operations. Mechanical dredges are particularly efficient on dredging projects where the placement site is several miles away.
Clamshell dredges are designed to handle loose to medium dense soils and dredge materials, while backhoe and dipper dredges are used to remove consolidated or hard-packed materials and can also be used to clear rock and debris. Hooded or enclosed buckets are utilized to control the flow of water and to prevent contaminated sediments from seeping back into the water column.